針對鈷冶煉中排出的高鎂硫酸銨廢水,以硫化鈉為沉淀劑去除鈷鎳,采用磷酸二氫銨除鎂+四效逆流降膜真空蒸發(fā)法組合工藝,可綜合回收硫化鈷與硫化鎳、磷酸銨鎂、硫酸銨,其中磷酸銨鎂和硫酸銨產品均達到國家一級標準,最終廢水中氨氮≤ 8 mg/L。生產實踐表明:年處理30萬t高鎂硫酸銨廢水,可回收300 t硫化鎳鈷,1.6萬t六水磷酸銨鎂及4萬t硫酸銨,年銷售收入達600萬元以上,實現(xiàn)了高鎂氨氮廢水的資源化。
鈷濕法冶煉過程中會產生硫酸銨廢水。由于鈷原料的變化,硫酸銨廢水中除含有高濃度氨氮外,常含有大量重金屬離子如鎳、鈷、鎂等。含鎂硫酸銨廢水中的氨氮主要以NH4+形式存在,易導致水體富營養(yǎng)化。氨氮廢水處理方法如吹脫法、沸石脫氨法、折點加氯法等難以處理高濃度氨氮廢水,也無法處理金屬離子,廢水很難達到排放標準。此外,由于硫酸銨廢水含有大量金屬離子,有廠家采用濃縮結晶回收硫酸銨的方法或萃取提純后再濃縮結晶回收硫酸銨方法進行處理,直接結晶回收的硫酸銨含鎂雜質較高,市場銷售前景不太樂觀,致使工廠回收的硫酸銨大量堆積存放;而使用萃取法預先分離金屬離子再濃縮結晶回收硫酸銨,因廢水量增大,氨氮濃度高,運行成本廠家一般難以接受,因此該工藝難以實現(xiàn)工業(yè)化。
磷酸銨鎂(MgNH4˙PO4)沉淀法,它是通過添加沉淀劑使廢水中的氨氮沉淀為磷酸銨鎂,達到廢水脫氮的目的。20世紀90年代該方法作為一種新的廢水處理工藝而迅速興起,并進入到應用階段。贛州逸豪優(yōu)美科實業(yè)有限公司技術人員根據廢水特點,采用磷酸二氫銨除鎂與四效逆流降膜真空蒸發(fā)器相結合工藝,對鈷冶煉高鎂硫酸銨廢水進行預處理,然后采用沉淀法除鎂,最后采用四效蒸發(fā)硫酸銨廢水濃縮結晶,回收銨鹽產品,最終廢水氨氮≤8 mg/L,出水可完全回用或達到國家標準排放。生產實踐表明,年處理30萬t高鎂硫酸銨廢水可回收300 t硫化鎳鈷、1.6萬t磷酸銨鎂及4萬t硫酸銨,年收入達600萬元。該技術不但可解決高鎂氨氮廢水的污染問題,還能獲得不錯的經濟效益,實現(xiàn)氨氮廢水的資源化。
01、生產概況
該公司鈷冶煉采用萃取凈化工藝,主要生產工藝流程如圖 1所示。
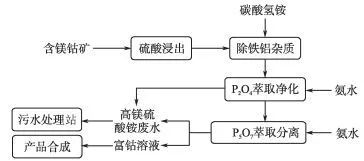
圖 1 鈷冶煉生產工藝流程
由圖 1可知,鈷冶煉過程中排放大量高鎂硫酸銨廢水,主要來源于萃取過程的萃余液,其中鎂來源于鈷礦浸出,高濃度氨氮來源于浸出工序的除雜單元與萃取的銨皂單元。據統(tǒng)計,每生產1 t鈷金屬產品,產生約60 m3含鎂硫酸銨廢水。如果處理不當,該廢水對環(huán)境尤其是水體會造成嚴重污染。該含鎂硫酸銨廢水主要成分:NH4+為26.17 g/L,Co為0.05 g/L,Ni為0.67 g/L,Mg為5.5 g/L,pH為5~6。
經分析,廢液主要由氨氮和金屬離子(主要是鈷、鎳、鎂)組成,鈷與鎳采用添加硫化鈉沉淀法去除,鎂離子采用MAP法回收磷酸銨鎂,經提純后的硫酸銨廢水再經四效逆流降膜真空蒸發(fā)器制備硫酸銨產品。高鎂硫酸銨廢水處理流程如圖 2所示,四效逆流降膜式設備連接情況見圖 3。
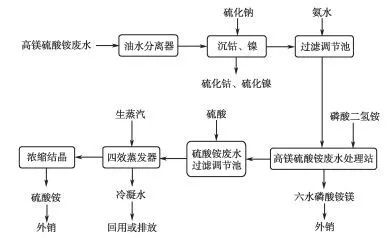
圖 2 高鎂硫酸銨廢水處理工藝流程
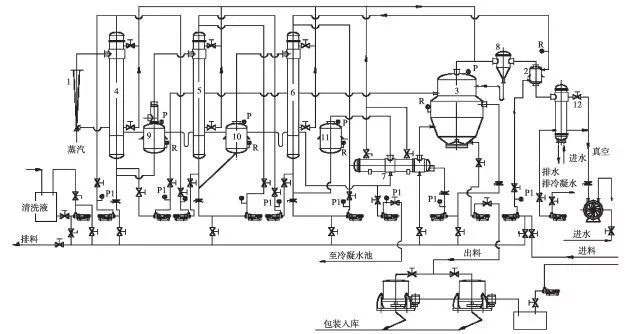
圖 3 四效逆流降膜式設備連接
萃取單元產生的高鎂硫酸銨廢水預經油水分離器除去有機相,然后用硫化鈉沉淀廢水中的鈷、鎳,濾渣返回生產系統(tǒng)再處理,濾液進入貯水池中,用氨水調節(jié)廢液pH至8.0~10.0,通過磷酸二氫銨除鎂至1 mg/L以下,固液分離后濾液用硫酸回調pH至7.0以下,進入四效逆流降膜蒸發(fā)器進行濃縮,結晶分離,最后制得硫酸銨產品。
硫酸銨廢水制備硫酸銨晶體具體流程:調好硫酸銨廢液pH后,經泵加壓先進入到螺旋板式預熱器進行預熱,隨后進入Ⅲ效蒸發(fā)器蒸發(fā)掉部分水分后,沸騰的硫酸銨液體進入三效分離罐,使硫酸銨液與二次汽分離,分離后的硫酸銨液由Ⅲ效泵采出,經預熱器預熱后依次進入Ⅱ、Ⅰ效蒸發(fā)器,從界區(qū)外來的高壓蒸汽進入Ⅰ效蒸發(fā)器殼程內,冷凝液排入阻汽排水罐排出,排出的蒸汽冷凝液經換熱后進入蒸汽冷凝液罐。Ⅱ效的二次汽經增濕后進入Ⅲ效蒸發(fā)器作為該效的熱源,Ⅲ效的二次汽經增濕后進入Ⅳ效蒸發(fā)器作為該效的熱源,使硫酸銨液進一步濃縮。硫酸銨液濃縮至一定濃度后進入結晶鍋,當結晶鍋內硫酸銨液波美度為45~50時,打開出料閥門進行出料,進入臥式螺旋離心機,將結晶后的硫酸銨從濃縮液中分離出來,并將干燥后的硫酸銨產品包裝入庫。分離后的液體回到母液池再次濃縮,該工藝產生的冷凝水可直接回用或排放。
02、產品與冷凝水主要成分及操作工藝參數
該工藝中回收的產品有硫化鈷與硫化鎳混合物、六水磷酸銨鎂與硫酸銨產品。硫化鈷鎳混合物返回生產系統(tǒng)再分離回收,六水磷酸銨鎂與硫酸銨產品外銷。四效蒸發(fā)器產生的冷凝水返回生產系統(tǒng)或直接外排。硫化鈷鎳混合物中Co占11.25%、Ni占28.45%、NH4+占0.15%、H2O占2.80%。磷酸銨鎂、硫酸銨與冷凝水的成分見表 1~表 3。
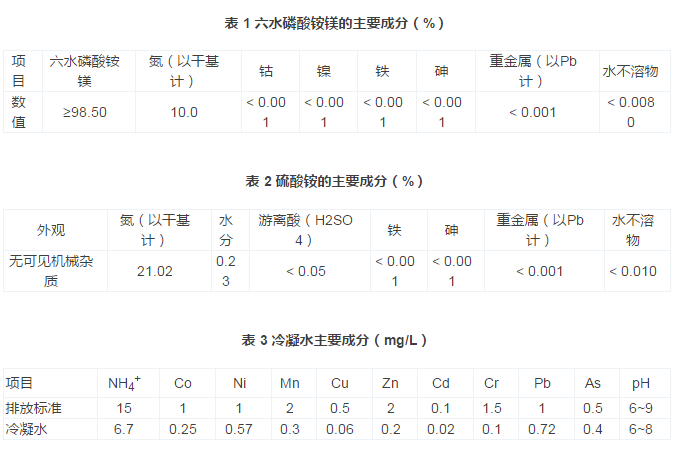
排放標準參考GB 8978—1996《污水綜合排放標準》。由表 3可見,經該工藝處理后,排放廢水各項指標達到了污水綜合排放要求,為節(jié)約水資源,冷凝水一般返回作浸出工序用水。
表 4為硫酸銨廢水處理工藝的主要操作參數。
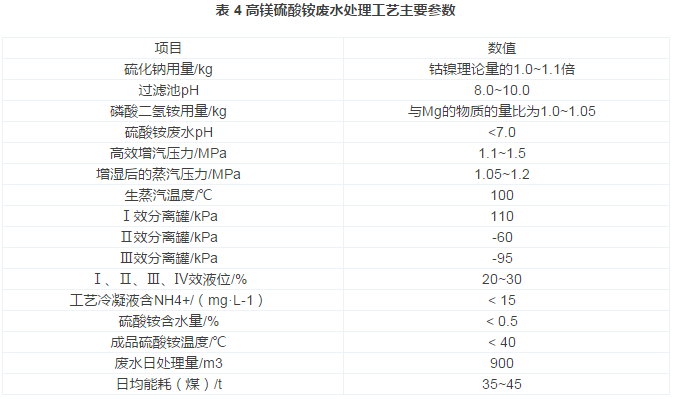
03、主要經濟指標
項目設計年處理30萬t高鎂硫酸銨廢水,年回收300 t硫化鎳鈷、1.6萬t磷酸銨鎂及4萬t硫酸銨產品,年利潤達600萬元以上,并達到了節(jié)水、節(jié)能、資源綜合利用的社會效益,其主要技術經濟指標如表 5所示。
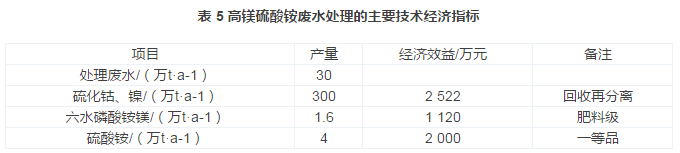
對目前常用的高鎂硫酸銨廢水處理方法進行比較,如表 6所示。
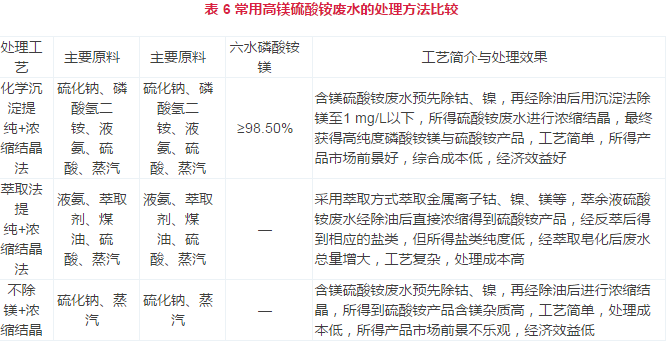
04、技術特點及優(yōu)勢
硫化鈉除鈷鎳、磷酸氫二銨除鎂及四效連續(xù)蒸發(fā)濃縮結晶結合工藝不但解決了高鎂硫酸銨廢水難以處理的問題,還取得不錯的經濟效益。與萃取提純+濃縮結晶法、直接濃縮結晶法、硝化/反硝化、離子交換法、堿性蒸氨法、折點加氯法及傳統(tǒng)工藝(氫氧化鈣沉淀硫酸根—空氣吹脫脫氨—A/O工藝去除COD組合處理技術)相比有以下優(yōu)勢:
(1)預先沉鈷鎳、磷酸氫二銨除鎂與四效連續(xù)蒸發(fā)濃縮結晶結合工藝的處理過程中無二次污染,有價資源可完全回收。
(2)該工藝不但回收了廢水中的鈷鎳,還回收了六水磷酸銨鎂與硫酸銨產品等副產品,達到廢水“零排放”要求。所得六水磷酸銨鎂質量分數達到98.5%以上,硫酸銨產品符合國家標準一等品(氮≥21%),可以直接用作農業(yè)肥料或冶金化工原料等。與萃取提純+濃縮結晶法、直接濃縮結晶法相比,該工藝運行成本更加低廉,還能獲得一定經濟效益,易于實現(xiàn)工業(yè)化。
(3)采用四效逆流降膜真空蒸發(fā)回收硫酸銨晶體,流程短,操作方便且簡單、能耗低,并采用先進的DCS操作控制系統(tǒng),料液濃度可隨意控制且相對穩(wěn)定,有效解決了含硫酸銨或氯化銨工業(yè)廢水蒸發(fā)過程中能耗過高、設備腐蝕等技術難點。四效連續(xù)蒸發(fā)濃縮結晶裝置采用國際先進的Ⅳ效逆流降膜式工藝,能滿足連續(xù)進料、連續(xù)排料的工藝要求,與蒸發(fā)器的強制循環(huán)形成最佳配合,資源利用率高、操作便捷、連續(xù),管理方便。
05、結論
(1)硫化鈉沉鈷鎳、磷酸氫二銨除鎂與四效連續(xù)蒸發(fā)濃縮結晶結合工藝回收硫酸銨是可行的,不但解決了高鎂硫酸銨廢水處理難題,還可回收廢水中的鈷鎳、六水磷酸銨鎂與硫酸銨產品等副產品。年處理30萬t高鎂硫酸銨廢水,最終廢水氨氮≤8 mg/L,可回收300 t硫化鎳鈷、1.6萬t 磷酸銨鎂及4萬t 硫酸銨,所得六水磷酸銨鎂質量分數達到98.5%以上,硫酸銨產品符合國家標準一等品要求,年銷售收入達600萬元以上,取得不錯的經濟效益,實現(xiàn)了氨氮廢水資源化。
(2)該工藝采用3個簡單工藝組合,解決了高鎂氨氮廢水難題,處理過程中無二次污染,廢水中氨氮等有價資源完全回收,達到廢水“零排放”要求。裝置具有能夠長期運行的優(yōu)點,適合工業(yè)化生產。
來源:工業(yè)水處理 作者:劉東輝等
特此聲明:
1. 本網轉載并注明自其他來源的作品,目的在于傳遞更多信息,并不代表本網贊同其觀點。
2. 請文章來源方確保投稿文章內容及其附屬圖片無版權爭議問題,如發(fā)生涉及內容、版權等問題,文章來源方自負相關法律責任。
3. 如涉及作品內容、版權等問題,請在作品發(fā)表之日內起一周內與本網聯(lián)系,否則視為放棄相關權益。