城市生活垃圾焚燒飛灰中常含有大量的具有高浸出毒性的可溶性重金屬,其含量比一般土壤中高10~100倍,如對(duì)這些飛灰采取簡(jiǎn)單的填埋處理,勢(shì)必增加對(duì)生態(tài)環(huán)境的污染,嚴(yán)重威脅人類的生存和生活環(huán)境[1]。與此同時(shí),焚燒飛灰主要化學(xué)組成屬CaO-SiO2-Al2O3體系,已有研究表明,利用焚燒飛灰輔以其他校正原料煅燒,不僅可以制備硅酸鹽水泥,還可制備以無水硫鋁酸鈣或阿利尼特等為主的節(jié)能水泥[2-5]。
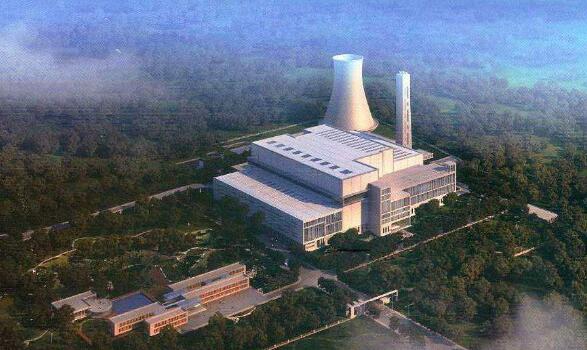
本文在已有研究基礎(chǔ)上,采取適宜率值在低于硅酸鹽水泥熟料燒成溫度下制備硫鋁酸鹽水泥熟料,高溫去除飛灰中劇毒性有機(jī)物的同時(shí),重點(diǎn)研究燒成過程中重金屬的逸放及其在硬化水泥漿體中的浸出特性,為焚燒飛灰在水泥工業(yè)中資源化利用的可行性及安全性提供依據(jù)。
1 試驗(yàn)材料與方法
1.1 原材料
試驗(yàn)采用垃圾焚燒飛灰的XRD圖譜見圖1。從圖1可知,其主要物相包括KCl、NaCl、Ca(OH)2、CaCl2、CaClOH、CaSO4、CaCO3、SiO2和CaO等。校正原料包括石灰石粉、鋁礬土和脫硫石膏。采用X射線熒光光譜(XRF)測(cè)得的原料化學(xué)成分見表1。
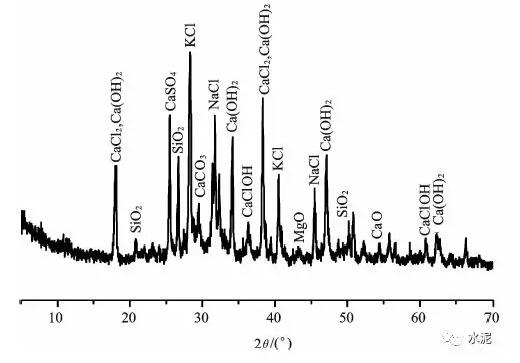
圖1 垃圾焚燒飛灰XRD分析
表1 試驗(yàn)用原料的主要化學(xué)組成 %
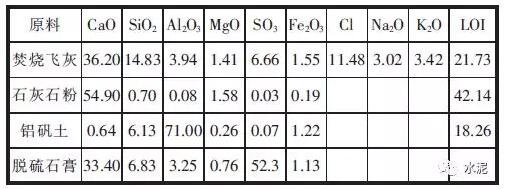
1.2 試驗(yàn)方法
在已有研究基礎(chǔ)上,控制堿度Cm、鋁硫比P和鋁硅比n分別為1.05、2.5和3,焚燒飛灰在原料中的摻量為30%。原材料按比例混合均勻后置于Φ30mm×50mm圓形試模中,在200kN壓力下,穩(wěn)壓2min后卸壓。將所得試樣放入高溫爐中以30℃/min勻速升溫至1250℃并保溫2h。采用X射線衍射儀(XRD)和X射線熒光光譜(XRF)對(duì)燒成熟料礦物及化學(xué)組成進(jìn)行分析。
將無水石膏按不同摻量與磨細(xì)硫鋁酸鹽水泥熟料充分混合,以0.3為水灰比拌合成型凈漿試樣,在(20±2)℃、相對(duì)濕度95%條件下養(yǎng)護(hù)至設(shè)定齡期,測(cè)試其抗壓強(qiáng)度,并采用XRD對(duì)硬化漿體的礦物組成進(jìn)行分析。
對(duì)燒制水泥熟料和焚燒飛灰中的重金屬含量進(jìn)行測(cè)定。將試樣粉磨至全部通過0.08mm的方孔篩,準(zhǔn)確稱取粉末適量,采用HF-HNO3-HClO4聯(lián)合消解法消解后定容,使用等離子原子發(fā)射光譜儀(ICP-AES)測(cè)定各樣品中的Zn、Cu、Cd、Ni、Cr和Pb重金屬元素含量。
對(duì)含5%無水石膏的硫鋁酸鹽水泥水化28d試樣,分三組進(jìn)行重金屬浸出試驗(yàn):第一組參照GB5086.2—1997《固體廢物浸出毒性浸出方法 水平振蕩法》進(jìn)行,硬化水泥漿體破碎并過5mm篩,顆粒隨即轉(zhuǎn)入600ml含去離子水廣口聚乙烯瓶中;第二組參照TCLP 1311(美國(guó)標(biāo)準(zhǔn)毒性浸出方法)進(jìn)行,樣品準(zhǔn)備過程與第一組相同,浸出液則采用pH值為2.8醋酸;第三組試樣則不經(jīng)破碎,直接浸泡在去離子水中,并參照GB7023《放射性廢物固化體長(zhǎng)期浸出試驗(yàn)》進(jìn)行。第一、二組試樣經(jīng)振蕩器振蕩8h,靜置16h,第三組試樣浸泡至28d,均采用中速定量濾紙進(jìn)行過濾,濾液經(jīng)定容后用ICP-AES測(cè)定重金屬離子含量。
2 結(jié)果與討論
2.1 硫鋁酸鹽水泥熟料的組成
經(jīng)1250℃煅燒2h后所得硫鋁酸鹽水泥熟料的XRD分析結(jié)果見圖2。由圖2可知,熟料中的主要礦物為C4A3S、C2S和少量CaSO4。表2為熟料XRF分析結(jié)果,在此基礎(chǔ)上結(jié)合物相組成,采用鮑格公式對(duì)熟料的礦物組成進(jìn)行計(jì)算,具體結(jié)果為:C4A3S:70%;C2S:26%;CaSO4:4%。
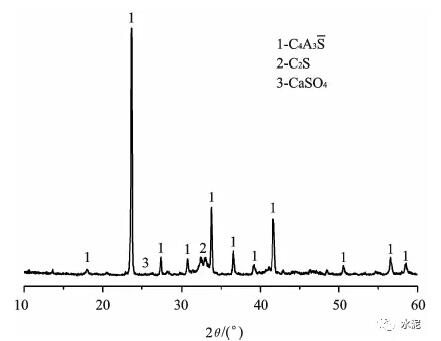
圖2 硫鋁酸鹽水泥熟料XRD分析
表2 硫鋁酸鹽水泥熟料的主要化學(xué)組成 %

2.2 石膏對(duì)硫鋁酸鹽水泥性能的影響
石膏摻量分別為0%、5%、10%、20%時(shí),配制硫鋁酸鹽水泥各齡期的抗壓強(qiáng)度見圖3。未摻石膏的試樣在水化前3d均強(qiáng)度太低且增長(zhǎng)十分緩慢,但是后期強(qiáng)度發(fā)展較快。摻5%石膏時(shí),各齡期強(qiáng)度理想,到56d時(shí)強(qiáng)度依然保持增長(zhǎng)的趨勢(shì)。而石膏摻量增至10%時(shí),雖然水化早期(1d)強(qiáng)度較高,但后期強(qiáng)度增長(zhǎng)較慢。當(dāng)石膏摻量增至20%時(shí),各齡期強(qiáng)度均有所降低。
由于石膏對(duì)硫鋁酸鹽水泥水化起到至關(guān)重要作用,采用XRD對(duì)摻5%石膏硬化水泥漿體的礦物組成進(jìn)行分析,結(jié)果見圖4。由圖4可知,水化3d后,漿體中便有大量AFt生成;水化28d后,C4A3S 的主要特征峰高度較3d時(shí)顯著下降,AFt特征峰略有提高。石膏摻量在很大程度上決定熟料中C4A3S 的水化程度和鈣礬石等水化產(chǎn)物的形成量。
不摻加石膏時(shí),水化形成鈣礬石所需硫質(zhì)來源于熟料本身,因而純熟料早期的水化速度較慢。加入石膏后,C4A3S 水化速度大大加快,但石膏摻量存在一個(gè)限值,當(dāng)摻量過大時(shí),水泥石后期強(qiáng)度反而發(fā)展緩慢。
這是因?yàn)樵谒跗?,鈣礬石生成促進(jìn)了強(qiáng)度的發(fā)展,當(dāng)水泥石達(dá)到一定的強(qiáng)度后,再生成的過量AFt和二次石膏會(huì)造成膨脹,使已達(dá)穩(wěn)定結(jié)構(gòu)的水泥石結(jié)構(gòu)疏松、孔隙率增加,導(dǎo)致強(qiáng)度反而有所降低。此外,熟料中C2S持續(xù)水化也有助于水泥后期強(qiáng)度的穩(wěn)定發(fā)展。
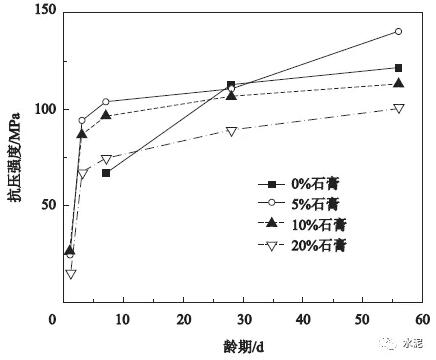
圖3 石膏摻量對(duì)硫鋁酸鹽水泥抗壓強(qiáng)度的影響
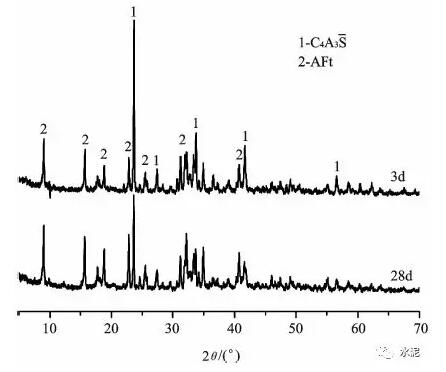
圖4 硬化硫鋁酸鹽水泥漿體的XRD圖
2.3 煅燒過程中重金屬的揮發(fā)
排入大氣中的重金屬元素會(huì)直接對(duì)環(huán)境和人類產(chǎn)生威脅,因此利用垃圾焚燒飛灰煅燒水泥時(shí),需對(duì)重金屬元素在水泥熟料中的固化率進(jìn)行研究。除對(duì)煅燒出的硫鋁酸鹽水泥熟料進(jìn)行分析外,同時(shí)將垃圾焚燒飛灰按照與熟料相同的熱工制度進(jìn)行煅燒并分析其重金屬元素含量,以比較燒成的水泥熟料對(duì)重金屬元素的固化效果。重金屬在水泥中的固化率可按式(1)進(jìn)行計(jì)算[6],重金屬測(cè)得值及其固化率計(jì)算結(jié)果如表3所示。
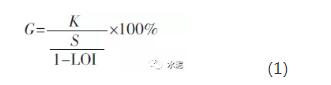
式中:
G——重金屬在熟料中的固化率,%;
K——熟料中重金屬元素含量,mg/g;
S——生料中重金屬元素含量,mg/g;
LOI——生料燒失量。
由表3可知,原料垃圾焚燒飛灰于1250℃單獨(dú)煅燒后Pb幾乎全部釋放,Zn和Cd只有少量殘留,Cu的固化率不到10%,Cr的固化率超過80%,Ni只有少部分揮發(fā)。而輔以其他原料煅燒制得的硫鋁酸鹽水泥熟料中,Ni、Cr和Zn的固化效果最好;Cu和Cd大部分揮發(fā),固化效果較差;熟料對(duì)Pb的固化效果最差,只有3.9%的Pb固化在熟料中。
焚燒飛灰中含有氯會(huì)對(duì)重金屬的揮發(fā)產(chǎn)生影響,如CdCl2和PbCl2分別在960℃和950℃便會(huì)揮發(fā)[7-8]。此外,除原材料組成外,重金屬的揮發(fā)特性還受到煅燒制度和窯內(nèi)環(huán)境等因素的共同影響。
表3 煅燒后重金屬含量及其固化率
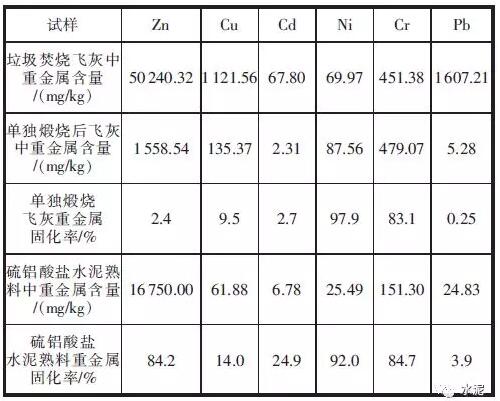
2.4 硬化水泥漿體中重金屬的浸出
采用三種浸出試驗(yàn)方法測(cè)得硬化水泥漿體中重金屬浸出濃度結(jié)果見表4,三種方法同時(shí)考慮材料不同服役狀態(tài)(方法一、二為破壞后,方法三為正常狀態(tài)下),以及環(huán)境因素的影響。表4同時(shí)給出不同地區(qū)關(guān)于重金屬濃度浸出限值要求。
從表4可以看出,第三組未經(jīng)破壞的硬化水泥漿體中,其重金屬浸出量甚至低于儀器的檢出限。由于硫鋁酸鹽水泥主要水化產(chǎn)物為鈣礬石,其晶體結(jié)構(gòu)特征表現(xiàn)為六角棱柱或柱狀,這種柱狀結(jié)構(gòu)中Ca2+、Al3+、SO42-和OH-可通過離子取代固結(jié)部分有害離子,如Cr等[9-11]。
此外,C2S水化生成的C-S-H凝膠可通過吸附等方式進(jìn)一步固化重金屬離子。研究發(fā)現(xiàn),硬化硫鋁酸鹽水泥漿體的pH值在10~11左右,堿度較硅酸鹽水泥低,可降低重金屬離子的溶解度[12-13]。
比較第一和第二組重金屬浸出濃度測(cè)試結(jié)果發(fā)現(xiàn),采用醋酸作浸出液的第二組試樣中重金屬浸出濃度較高。醋酸環(huán)境一方面使得Cr、Cu、Cd、Zn和Pb等重金屬溶解度增加[14];另一方面對(duì)硬化漿體造成腐蝕形成五水乙酸鈣,使得鈣礬石發(fā)生分解生成石膏和鋁膠,從而降低體系固結(jié)重金屬能力[15]。
采用三種浸出方法測(cè)得重金屬浸出濃度均低于不同標(biāo)準(zhǔn)規(guī)定限值。綜上可知,采用垃圾焚燒飛灰煅燒硫鋁酸鹽水泥,可溶性重金屬活動(dòng)態(tài)大大降低,其浸出量遠(yuǎn)遠(yuǎn)低于浸出毒性鑒別標(biāo)準(zhǔn),重金屬的浸出是一個(gè)緩慢浸取、緩慢稀釋的過程。但由于水泥基材料應(yīng)用廣泛,使用環(huán)境千差萬別,還應(yīng)進(jìn)一步研究利用垃圾焚燒飛灰燒制硫鋁酸鹽水泥在不同侵蝕環(huán)境下的浸出行為及其長(zhǎng)期應(yīng)用的安全性。
表4 不同方法測(cè)得硬化水泥漿中重金屬離子浸出濃度 (mg/kg)
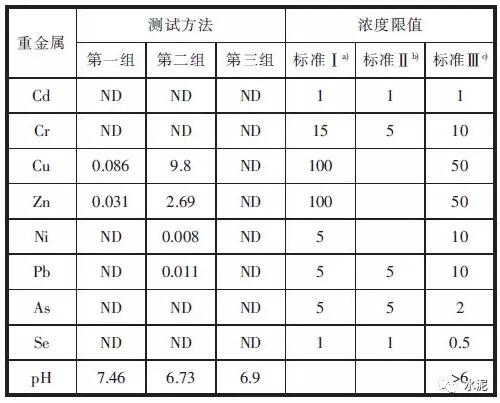
注:ND: 低于儀器測(cè)試限值 (<0.005mg/L);
a)中國(guó)國(guó)標(biāo)(GB 5085.3-2007,危險(xiǎn)廢物鑒別標(biāo)準(zhǔn));
b)美國(guó)標(biāo)準(zhǔn)毒性浸出方法有關(guān)重金屬浸出濃度最高限值(TCLP-1311);
c)歐盟關(guān)于廢棄物無害化填埋要求(2003/33/EC)。
3 結(jié)論
1)以垃圾焚燒飛灰做原料,控制堿度Cm=1.05、鋁硫比P=2.5和鋁硅比n=3條件下,可煅燒制得以C4A3S和C2S為主要礦物的硫鋁酸鹽水泥熟料。
2)石膏的摻量在很大程度上決定熟料中C4A3S的水化程度和鈣礬石等水化產(chǎn)物的生成量,對(duì)硫鋁酸鹽水泥早期強(qiáng)度發(fā)揮起到至關(guān)重要的作用。
3)垃圾焚燒飛灰煅燒硫鋁酸鹽水泥熟料過程中,Ni、Cr和Zn揮發(fā)率最低,而Cu和Cd大部分揮發(fā),而熟料對(duì)Pb的固化效果最差,96%的Pb在熟料煅燒過程中揮發(fā)。
4)采用醋酸作浸出液相對(duì)去離子水,使得重金屬浸出濃度較高,但仍低于相關(guān)標(biāo)準(zhǔn)關(guān)于毒性浸出最高限值。硫鋁酸鹽水泥主要水化產(chǎn)物鈣礬石、C-S-H凝膠可通過離子取代和吸附等方式有效固化重金屬離子。但關(guān)于垃圾焚燒飛灰燒制硫鋁酸鹽水泥在不同使用環(huán)境中長(zhǎng)期應(yīng)用的安全性還有待進(jìn)一步研究。
特此聲明:
1. 本網(wǎng)轉(zhuǎn)載并注明自其他來源的作品,目的在于傳遞更多信息,并不代表本網(wǎng)贊同其觀點(diǎn)。
2. 請(qǐng)文章來源方確保投稿文章內(nèi)容及其附屬圖片無版權(quán)爭(zhēng)議問題,如發(fā)生涉及內(nèi)容、版權(quán)等問題,文章來源方自負(fù)相關(guān)法律責(zé)任。
3. 如涉及作品內(nèi)容、版權(quán)等問題,請(qǐng)?jiān)谧髌钒l(fā)表之日內(nèi)起一周內(nèi)與本網(wǎng)聯(lián)系,否則視為放棄相關(guān)權(quán)益。